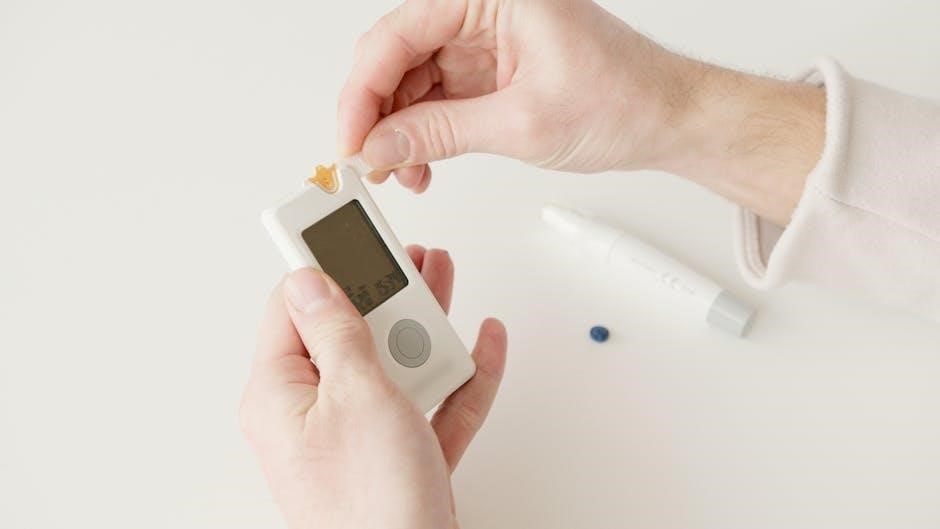
1756 if16 user manual
The Allen-Bradley 1756-IF16 is a key component in the ControlLogix series, offering precise analog input capabilities for industrial automation. Designed for flexibility and scalability, it integrates seamlessly with Rockwell Software solutions, ensuring efficient data acquisition and system control.
1.1 Overview of the Allen-Bradley 1756-IF16
The Allen-Bradley 1756-IF16 is a high-performance analog input module designed for the ControlLogix series. It offers 16 single-ended or 8 differential input channels, providing flexibility for various industrial applications. The module supports high-speed data acquisition, making it suitable for demanding control systems. With compatibility with RSLogix 5000 software, it ensures seamless integration and configuration. Its robust design and adherence to industry standards make it a reliable choice for precise data collection and processing in automation environments. The 1756-IF16 is widely used in process control, motion systems, and other industrial applications requiring accurate analog signal processing.
1.2 Importance in the ControlLogix Series
The 1756-IF16 plays a crucial role in the ControlLogix series by providing high-precision analog input capabilities. Its ability to handle both single-ended and differential inputs, along with high-speed data acquisition, makes it essential for applications requiring accurate and rapid signal processing. The module’s integration with RSLogix 5000 software enables efficient configuration and scalability, ensuring it meets the demands of modern industrial automation. Its reliability and compatibility with other ControlLogix components solidify its importance in building robust control systems across various industries.
1.3 Brief History and Development
The Allen-Bradley 1756-IF16 module was developed as part of Rockwell Automation’s commitment to advancing industrial control systems. Introduced in the early 2000s, it was designed to meet the growing demand for high-speed analog input capabilities in the ControlLogix platform. Building on the legacy of Allen-Bradley’s expertise, the module was engineered to provide precise data acquisition and integration with Rockwell Software tools like RSLogix 5000. Over the years, it has undergone enhancements to improve performance, compatibility, and safety standards, solidifying its role as a cornerstone in modern automation solutions.
Key Features and Specifications
The 1756-IF16 module offers 16 analog input channels, supporting both single-ended and differential inputs. It features high-speed data acquisition, compatibility with RSLogix 5000, and robust integration capabilities.
2.1 Input Channels and Types
The Allen-Bradley 1756-IF16 module provides 16 analog input channels, each capable of handling a wide range of signal types. It supports both single-ended and differential input configurations, offering flexibility for various industrial applications. Single-ended inputs are suitable for high-level signals, while differential inputs provide noise rejection and accuracy for low-level signals. This versatility allows the module to adapt to different system requirements, ensuring precise data acquisition in complex automation environments. The module’s design enables seamless integration with ControlLogix systems, making it a robust solution for industrial control applications.
2.2 Differential and Single-Ended Inputs
The 1756-IF16 module supports both differential and single-ended input configurations, providing flexibility for various industrial applications. Differential inputs offer enhanced noise immunity and higher accuracy, making them ideal for low-level signals in noisy environments. Single-ended inputs, while less immune to noise, are simpler to implement and suitable for high-level signals. The module allows users to configure channels to meet specific application requirements, ensuring optimal performance in diverse automation scenarios. This dual capability makes the 1756-IF16 a versatile solution for precise analog signal acquisition in industrial control systems.
2.3 High-Speed Input Capabilities
The 1756-IF16 module offers high-speed input capabilities, enabling fast and precise data acquisition in demanding industrial applications. With advanced sampling rates, it captures dynamic process changes accurately, making it ideal for high-frequency signal processing. High-speed inputs are configurable, allowing users to optimize performance for specific tasks. This feature is particularly beneficial in motion control systems, where real-time data processing is critical. The module’s high-speed capabilities ensure reliable operation in environments requiring rapid input processing, making it a robust solution for modern automation needs.
Installation and Wiring
Proper installation and wiring are crucial for optimal performance. Always consult the user manual for detailed diagrams and connection guidelines to ensure safe and reliable functionality.
3.1 Mounting and Placement Guidelines
Mount the 1756-IF16 module in a ControlLogix chassis, ensuring it is securely fastened. Place it in a well-ventilated area to prevent overheating. Avoid exposing it to direct sunlight or moisture. Maintain a minimum clearance of 2 inches around the module for proper airflow. Ensure the chassis is installed in a stable, vibration-free environment to prevent damage. Always follow the user manual’s specific mounting instructions for optimal performance and reliability. Proper placement ensures efficient operation and extends the module’s lifespan.
3.2 Wiring Diagrams and Terminal Connections
Refer to the user manual for detailed wiring diagrams and terminal connections. The 1756-IF16 module provides 16 analog input channels, with terminals labeled clearly for easy identification. Connect input signals to the appropriate terminals, ensuring proper grounding to avoid noise interference. Use shielded cables for high-speed inputs to maintain signal integrity. Follow the recommended wiring practices to prevent cross-talk and ensure accurate data transmission. Verify all connections before powering up the system to avoid malfunctions. Proper wiring is critical for optimal performance and reliability of the module in industrial automation systems.
Configuration and Setup
The 1756-IF16 module is configured using RSLogix 5000 software. Define channel parameters, scaling, and input types to match application requirements for accurate data acquisition and system control.
4.1 Using RSLogix 5000 for Configuration
RSLogix 5000 streamlines the configuration of the 1756-IF16 module. Users can define channel settings, enabling high-speed or differential inputs, and apply scaling factors. The software offers real-time diagnostics, ensuring accurate module setup. It supports the integration of advanced features like high-speed inputs and alarms. Configuration is intuitive, with wizards guiding users through parameter selection. This ensures compatibility with ControlLogix systems, optimizing performance and minimizing errors during commissioning. Proper setup is crucial for reliable operation, making RSLogix 5000 an essential tool for configuring the 1756-IF16 module effectively.
4.2 Channel Configuration and Scaling
Channel configuration and scaling are critical for optimizing the 1756-IF16 module’s performance. Each input channel can be individually configured for single-ended or differential modes to suit specific application needs. Scaling parameters allow users to map raw analog signals to engineering units, ensuring precise data representation. The module supports high-speed sampling rates, which can be enabled or disabled based on the application requirements. Proper scaling ensures accurate data interpretation, while channel configuration flexibility allows the module to adapt to various industrial automation scenarios, enhancing overall system accuracy and reliability in process control and monitoring applications.
Calibration and Maintenance
Regular calibration and maintenance of the 1756-IF16 module ensure optimal performance and accuracy. Proper procedures prevent signal degradation and ensure reliable operation, while consistent upkeep extends module lifespan and system functionality.
5.1 Calibration Procedures
The 1756-IF16 module requires precise calibration to maintain accurate analog input readings. Users should follow Rockwell Automation’s guidelines, starting with powering down the system and ensuring all safety protocols are met. Using RSLogix 5000, configure the module to calibration mode. Apply the specified reference voltage to the input channels and verify the readings through the software. Adjustments should be made carefully to avoid signal distortion. Calibration ensures optimal performance and data integrity, preventing errors in process control. Regular recalibration is recommended, especially after system modifications or upgrades. Always refer to the official user manual for detailed step-by-step instructions to ensure compliance with industry standards and maintain system reliability.
5.2 Routine Maintenance Tips
Regular maintenance is crucial to ensure the 1756-IF16 module operates reliably. Start by inspecting all terminal connections for tightness and cleanliness. Use compressed air to remove dust or debris from the module and terminals. Check for signs of wear or corrosion on cables and connectors. Update firmware periodically to access the latest features and improvements. Perform diagnostic checks using RSLogix 5000 to identify potential issues early. Test input channels for accuracy and ensure proper grounding to prevent noise interference. Schedule periodic system backups to protect configuration data. Refer to the user manual for detailed maintenance schedules and procedures to maintain optimal performance and extend the module’s lifespan.
Safety Considerations
Always follow safety guidelines when handling the 1756-IF16 module. Ensure proper grounding and installation to prevent electrical hazards. Verify intrinsic safety ratings for use in hazardous environments. Comply with industry standards and manufacturer recommendations to maintain system integrity and operator safety. Regular inspections and adherence to safety protocols are essential for reliable operation and protection against potential risks.
6.1 Intrinsic Safety Ratings
The 1756-IF16 module meets stringent intrinsic safety standards, ensuring safe operation in hazardous environments. It is designed to prevent ignition of flammable substances by limiting energy release. The module complies with global certifications, including ATEX and IECEx, for use in Zone 1 and Zone 2 areas. Proper installation and maintenance are crucial to maintaining these safety ratings. Users must adhere to the provided guidelines and industry standards to ensure the module’s safe performance. Always verify the ratings match the specific application requirements to prevent potential risks. Compliance with these standards ensures reliability and protection in demanding industrial settings.
6.2 Compliance with Industry Standards
The 1756-IF16 module adheres to multiple industry standards, ensuring reliability and compatibility across various applications. It meets IEC 61508 and EN ISO 13849-1 for functional safety, as well as UL and CSA certifications for North American markets. Compliance with these standards guarantees the module’s performance under diverse operating conditions. Additionally, it aligns with global regulations for electromagnetic compatibility, ensuring minimal interference with other devices. This comprehensive compliance ensures seamless integration into existing systems and meets the demands of modern industrial automation. Users can trust the module’s adherence to rigorous quality and safety benchmarks.
Integration with Control Systems
The 1756-IF16 module integrates seamlessly with ControlLogix systems, supporting EtherNet/IP and other industrial protocols for efficient communication and real-time data exchange. Compatible with RSLogix 5000.
7.1 Communication Protocols
The 1756-IF16 module supports various communication protocols, including EtherNet/IP and ControlNet, enabling seamless integration with ControlLogix systems. These protocols ensure high-speed data transmission and compatibility with Rockwell Automation’s software solutions. The module’s ability to operate in both single-ended and differential modes further enhances its versatility in industrial communication networks. By leveraging these protocols, users can achieve efficient and reliable data exchange across their automation systems. This ensures optimal performance and scalability in diverse industrial applications, making the 1756-IF16 a robust choice for modern control systems.
7.2 Network Integration and Compatibility
The 1756-IF16 module is designed for seamless integration into industrial networks, supporting popular protocols like DeviceNet, ControlNet, and EtherNet/IP. This ensures compatibility with a wide range of devices and control systems. Its ability to operate within Rockwell Automation’s ecosystem allows for effortless integration with tools like RSLogix 5000 and Studio 5000. The module’s compatibility extends to various I/O configurations, making it adaptable to diverse automation setups. This flexibility enables users to enhance scalability and efficiency in their industrial control systems, ensuring reliable performance across networked applications.
Diagnostics and Monitoring
The 1756-IF16 module features advanced diagnostics and monitoring capabilities, including status indicators and fault detection. Real-time monitoring ensures prompt issue identification and resolution, enhancing system reliability.
8.1 Status Indicators and LEDs
The 1756-IF16 module is equipped with status indicators and LEDs that provide visual feedback on module operation. These indicators show power status, communication activity, and fault conditions. Each LED corresponds to specific states, such as module OK, error, or communication active. By monitoring these indicators, users can quickly identify system status and troubleshoot issues without detailed manual checks. This feature enhances operational efficiency and ensures minimal downtime in industrial automation environments. Proper interpretation of LED statuses is essential for maintaining optimal system performance and addressing potential faults promptly.
8.2 Fault Detection and Alarms
The 1756-IF16 module incorporates advanced fault detection mechanisms to identify and alert users to potential issues. These include sensor faults, communication errors, and module malfunctions. Alarms are triggered for critical conditions, ensuring timely intervention. The module stores fault data for later analysis, aiding in troubleshooting and system optimization. Proper configuration of alarms is essential to prevent downtime and ensure reliable operation. Users can monitor these alerts through Rockwell Software tools, enabling proactive maintenance and minimizing operational disruptions. Regular review of fault logs is recommended to maintain system integrity and performance.
Module Comparison
The 1756-IF16 stands out for its high-speed differential inputs and flexibility, making it ideal for demanding applications compared to other modules in the ControlLogix series.
9.1 1756-IF16 vs. 1756-IF8
The 1756-IF16 and 1756-IF8 differ primarily in their input channel configurations. The 1756-IF16 offers 16 analog input channels, including 8 differential and 4 high-speed differential inputs, making it suitable for high-precision applications. In contrast, the 1756-IF8 provides 8 analog input channels with 4 differential inputs, ideal for smaller-scale systems. Both modules support single-ended and differential modes, ensuring flexibility in various industrial setups. The IF16’s additional channels and high-speed capabilities make it preferable for complex processes, while the IF8 is a cost-effective solution for simpler installations.
9.2 Comparison with Newer Models
Newer models in the ControlLogix series, such as the 1756-IF16K, offer enhanced features like improved diagnostics, higher-speed inputs, and better noise immunity. These advancements provide greater accuracy and reliability in industrial applications. While the 1756-IF16 remains a robust option, newer modules integrate more seamlessly with updated software and hardware, supporting modern automation demands. The choice between the IF16 and newer models depends on specific application requirements, with newer versions catering to more complex and high-performance systems.
Applications Across Industries
The Allen-Bradley 1756-IF16 module is widely used across various industries, including process control and motion systems, due to its high accuracy and reliability in data acquisition and system control.
10.1 Use in Process Control
The Allen-Bradley 1756-IF16 module is extensively utilized in process control systems for precise monitoring and regulation of analog signals. Its high accuracy and reliability make it ideal for applications involving temperature, pressure, and flow rate measurements. The module’s ability to handle both single-ended and differential inputs ensures flexibility in various industrial environments. Additionally, its integration with Rockwell Software enables seamless data acquisition and control, streamlining operations in sectors like chemical processing, oil & gas, and power generation. This module is essential for maintaining operational efficiency and safety in demanding process control scenarios, ensuring accurate and consistent performance.
10.2 Applications in Motion Systems
The 1756-IF16 module plays a crucial role in motion systems by providing high-precision analog input capabilities for motor control and synchronization. Its high-speed differential inputs enable accurate monitoring of position, velocity, and torque, ensuring smooth operation in servo and stepper motor applications. The module’s integration with Rockwell Software allows for real-time data processing and precise control, making it ideal for advanced motion systems. Its reliability and flexibility enhance performance in applications like robotics, CNC machines, and automated conveyor systems, ensuring seamless integration and optimal motion control capabilities in industrial automation environments.
User Feedback and Reviews
Users praise the 1756-IF16 module for its reliability and performance in industrial automation. Its ease of integration and robust feature set make it a preferred choice for precise control applications.
11.1 Industry Reception and Performance
The Allen-Bradley 1756-IF16 has received widespread acclaim for its exceptional performance and reliability in industrial automation. Users highlight its ability to deliver precise analog input capabilities, making it a cornerstone in process control and motion systems. Its seamless integration with Rockwell Software and compatibility with ControlLogix systems further enhance its reputation. Engineers and technicians appreciate its robust design and diagnostic features, ensuring minimal downtime and optimal productivity. Overall, the module is regarded as a reliable and efficient solution for demanding industrial applications, solidifying its position in the market.
11.2 Common User Issues and Solutions
Users of the 1756-IF16 module often encounter issues related to wiring, configuration, and high-speed mode errors. Improper terminal connections and misconfigured channels are frequent problems, which can be resolved by consulting the wiring diagrams in the user manual. High-speed mode errors often stem from incorrect module settings, requiring adjustment through RSLogix 5000. Additionally, users report occasional signal noise issues, which can be mitigated by using shielded cables and ensuring proper grounding. Regular firmware updates and adherence to Rockwell Automation guidelines help minimize downtime and ensure optimal performance.
The 1756-IF16 module is a robust solution for analog input needs, supported by extensive resources like the GuardLogix Controllers User Manual and Rockwell Automation support.
12.1 Summary of Key Points
The Allen-Bradley 1756-IF16 module is a high-performance analog input module designed for the ControlLogix series, offering 16 single-ended or 8 differential inputs. It supports high-speed capabilities, making it ideal for motion systems and process control. The module is compatible with RSLogix 5000 for configuration and integrates seamlessly with Rockwell Automation solutions; Its robust design ensures reliability across various industrial applications, while compliance with industry standards guarantees safety and efficiency. Proper installation, wiring, and maintenance are essential for optimal performance, as outlined in the GuardLogix Controllers User Manual.
12.2 Accessing the User Manual and Support
The GuardLogix Controllers User Manual (publication 1756-UM020) provides comprehensive details for the 1756-IF16 module, including specifications, installation, and troubleshooting. Users can access this document through Rockwell Automation’s official website or by contacting their local Allen-Bradley distributor. Additional support resources, such as technical documentation and software tools, are available via Rockwell Automation’s customer portal. For further assistance, users can reach out to Rockwell Automation’s sales representatives or authorized distributors. Ensure compliance with safety standards and proper installation procedures for optimal performance.
Leave a Reply
You must be logged in to post a comment.